Cut Resistant Gloves - The Ultimate Guide
In the realm of workplace health & safety, protecting workers' hands from cuts and lacerations is paramount. Cut resistant gloves stand as a frontline defence, offering vital protection to those working with sharp objects or in hazardous environments. Understanding the nuances of cut resistant glove ratings and levels, safety specifications, standards, and testing procedures associated with these gloves is crucial for ensuring compliant protection for workers.
In this cut protection glove guide you will learn all you need to ensure you and/or your employees are protected against cut hazards.
- Page Contents
- The EN 388 Safety Standard
- Cut Glove Specifications
- Materials & Fabrics
- Testing
- Applications
The Role of "EN 388 Protective Gloves against Mechanical Risks" Standard
Central to the regulation of cut resistant gloves in the United Kingdom is the EN 388 standard. This comprehensive standard lays down stringent requirements for testing and marking gloves designed for cut resistance.
EN 388 mandates that cut rated gloves undergo rigorous testing to assess their performance against mechanical risks. This includes cuts, abrasions, tears, and punctures.
There were updates to the gloves standards in 2016 and 2018. Testing procedures were changed to better simulate the real world and ensure accurate marking. It is now more properly known as the EN 388:2016+A1:2018 Protective Gloves against Mechanical Risks standard.
Understanding Cut Glove Safety Ratings
It's essential to decipher the markings on the gloves themselves when choosing the right cut resistant gloves. These specifications, indicate the gloves' resistance to cuts and lacerations.
The old markings
The old numerical scale ranged from 1 to 5, with higher numbers indicating greater levels of protection. For instance:
- Level 1: Provides basic protection, enduring one cutting cycle to full severance/penetration.
- Level 2: Offers moderate protection, withstanding two cutting cycles.
- Level 3: Provides substantial protection, resisting up to five cutting cycles.
- Level 4: Offers advanced protection, enduring ten cutting cycles.
- Level 5: Represents the highest level of protection, capable of withstanding 20 or more cutting cycles.
These standards are now deprecated. It is unlikely you will be supplied with new gloves carrying these coded ratings from a BSIF Registered Safety Supplier.
The new and much improved cut resistant glove standards
The EN 388:2016 standard introduced a significant update to the classification system for mechanical risks by introducing an additional cut scale from A to F. This expansion allowed for a more nuanced evaluation of a gloves' performance, particularly in terms of their resistance to cuts and abrasions.
Here's how a typical cut resistant glove marking will now look:
The example cut glove above is rated F.
See the 5 character code on the back of the glove? In that example it is 4X42F. The F is the cut resistance designation.
Here's a breakdown of the new cut rating system
- Abrasion Resistance: This parameter measures the glove's resistance to abrasion. Performance is rated on a scale from 0 to 4, where 4 indicates the highest level of resistance. The above glove is rated 4 for abrasion resistance.
- Blade Cut Resistance: Reflecting advancements in testing methodologies, this scale assesses the glove's ability to withstand cuts from sharp blades. The rating ranges from 0 to 5, with 5 indicating the highest level of protection against blade cuts. This is to the old scale, so may contain a number, or as in the example above, it could be an X to show it was not tested in the old scale.
- Tear Resistance: Evaluating the glove's resistance to tearing, this scale provides a rating from 0 to 4. The above glove is rated 4 for tear resistance.
- Puncture Resistance: This scale measures the glove's ability to resist punctures from sharp objects, with ratings ranging from 0 to 4. The above glove is rated 2 for puncture resistance.
- Cut Resistance in Accordance with ISO 13997: This scale provides an alternative method for assessing cut resistance, particularly for materials where the traditional Coupe Test may not be suitable. It rates gloves from A to F, with F indicating the highest level of cut resistance according to the ISO 13997 testing method.
The above glove is rated F for cut resistance, the highest level of protection.
This updated classification system offers a more comprehensive evaluation of a gloves performance across various mechanical risks. This provides users with valuable information to make informed decisions regarding hand protection in the workplace.
Cut resistant gloves are tested to a minimum performance level. If you are not sure of the required cut protection level you need, choose the next level up.
Find a more comprehensive guide to calculating your required cut level in our article: how to choose the correct cut glove level.
Materials and Fabrics
What are cut resistant gloves made of? Cut resistant gloves are manufactured from a diverse array of materials and fabrics, each chosen for its specific properties and performance attributes.
Manufacturers commonly use high-performance fibres like Kevlar®, Dyneema®, and Spectra® due to their exceptional strength, durability, and resistance to cuts and abrasions. Additionally, gloves may feature coatings of nitrile or stainless steel for enhanced protection and grip in various working conditions.
Glass fibre yarn offers a surprising tensile strength and alone offers up to level B resistance to cutting. Crushed Basalt rock can be woven into filaments that offer a higher cut resistance to glass.
Any of the above materials can be mixed and woven together to create a stronger fabric.
Testing Procedures for Compliance
Ensuring the effectiveness of cut resistant gloves necessitates rigourous testing procedures.
The EN 388 standard employs several testing methods to evaluate gloves' resistance to mechanical risks. The Coupe Test is used to assess abrasion resistance, while the ISO 13997 TDM-100 Test determines the force required to cut through the glove material.
The Coupe Test
The standard method for assessing the abrasion resistance of glove materials is the Coupe Test. This test subjects glove materials to repeated rubbing against a rotating abrasive surface. It provides valuable data on the durability and longevity of glove materials under simulated wear conditions.
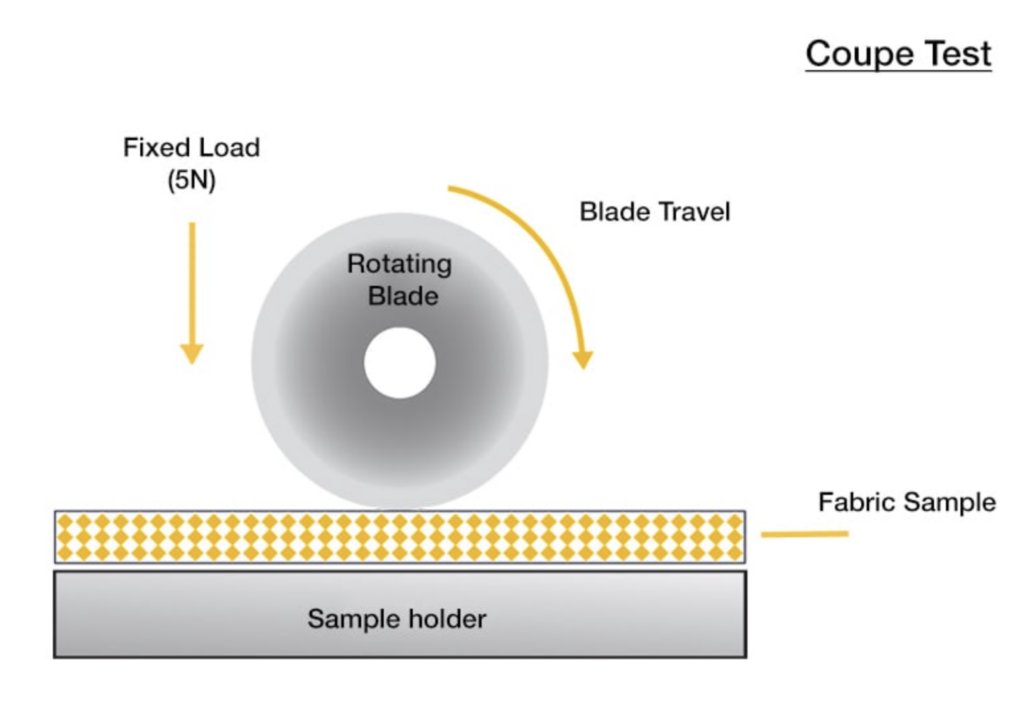
The test is typically conducted using an abrasion machine equipped with a rotating drum or abrasive surface. Gloves to be tested are securely mounted onto holders or fixtures within the machine, ensuring consistent testing conditions.
The rotating drum or abrasive surface applies a constant rotational force to the surface of the glove material. As the glove material rubs against the abrasive surface, frictional forces are generated, simulating wear and tear over time.
Gloves are visually inspected for signs of wear after testing, looking for problems such as surface abrasion, loss of material, or visible damage. The results of the Coupe Test provide a quantitative measure of the glove's abrasion resistance, typically reported as the number of cycles completed before a specified endpoint is reached. A higher number of cycles indicates greater abrasion resistance and durability.
ISO 13997 TDM-100 Test
The ISO 13997 TDM-100 test evaluates the resistance of glove materials to cuts and slashes by measuring the force required to penetrate through them with a rotating blade. It provides a quantitative measure of a glove's ability to withstand sharp object penetration, aiding in determining its level of cut resistance.
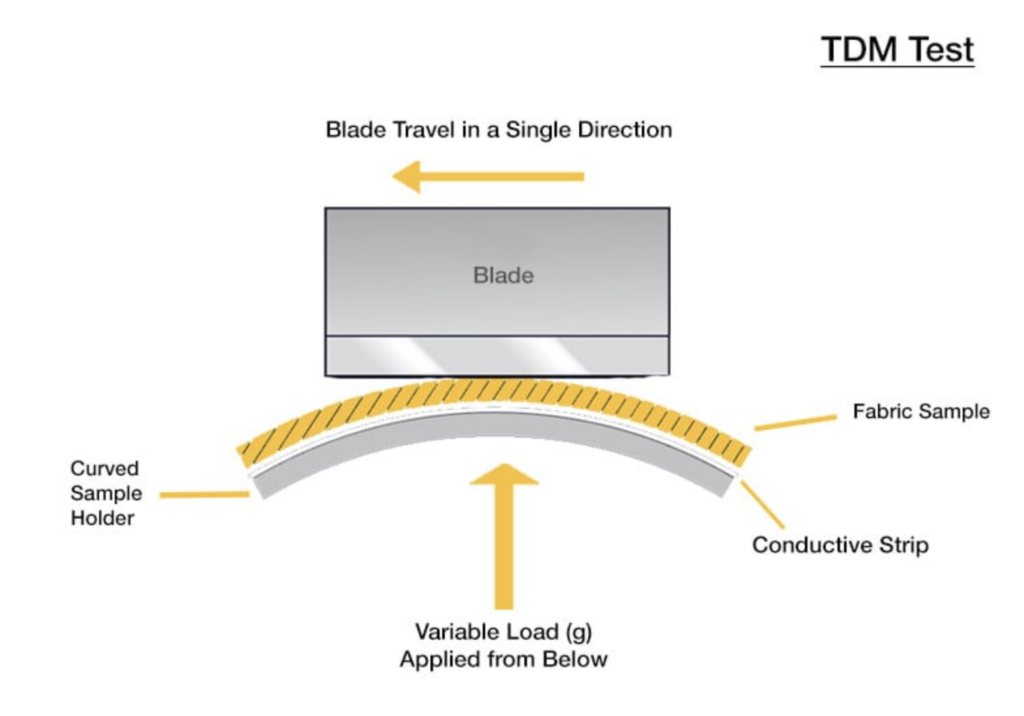
A TDM-100 machine which was specifically designed for this purpose, is typically used to conduct this test. The machine consists of a test fixture, a blade holder, and a cutting blade. To ensure consistent testing conditions, glove samples are securely mounted onto the test fixture.
A blade with a specified geometry and sharpness is attached to the machine and driven into the glove material at a controlled speed and force. As the blade penetrates the glove material, shearing forces are generated, simulating the action of a sharp object slicing through the material.
The ISO 13997 TDM-100 test employs standardised blades with defined geometry and cutting edges to ensure consistency and reproducibility of test results. The blade typically has a straight edge and is made of a hard material such as steel or tungsten carbide.
After testing, the glove samples are inspected for cuts, slashes, or penetrations. The test results are recorded and used to determine the glove's cut resistance rating.
The force required to cut through the material is typically reported in Newtons (N) or grams (g). A higher force value indicates greater cut resistance and protection.
Tear Resistance Test
This evaluates the glove's ability to resist tearing, providing insights into its durability under stress. Tear resistance testing evaluates a glove's ability to resist tearing or ripping when subjected to external forces.
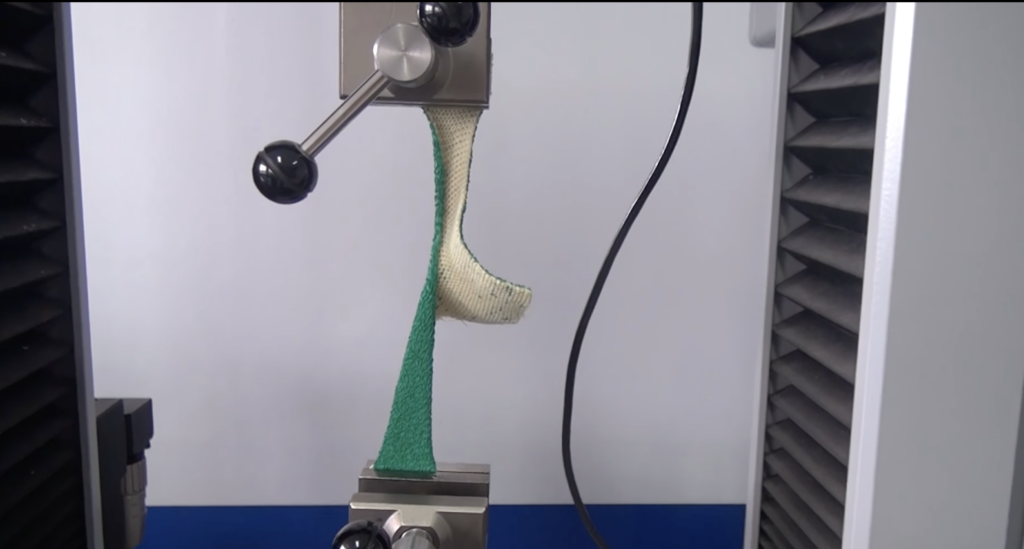
Glove samples are securely clamped between grips or jaws attached to the testing machine, ensuring uniform distribution of force during testing. This machine applies controlled tensile forces to the glove material, pulling it apart to induce tearing.
A higher tear resistance value indicates greater resistance to tearing or ripping, which translates to better performance and protection in real-world applications.
Puncture Resistance Test
Assessing the glove's resistance to punctures from sharp objects, this test helps determine its suitability for environments with piercing hazards.
The fabric is stretched taught between 2 discs to clamp it in place. A standardised puncture probe is driven into the glove material with controlled force and velocity to test the puncture resistance. The force required to puncture the glove is measured, providing a quantitative assessment of its puncture resistance.
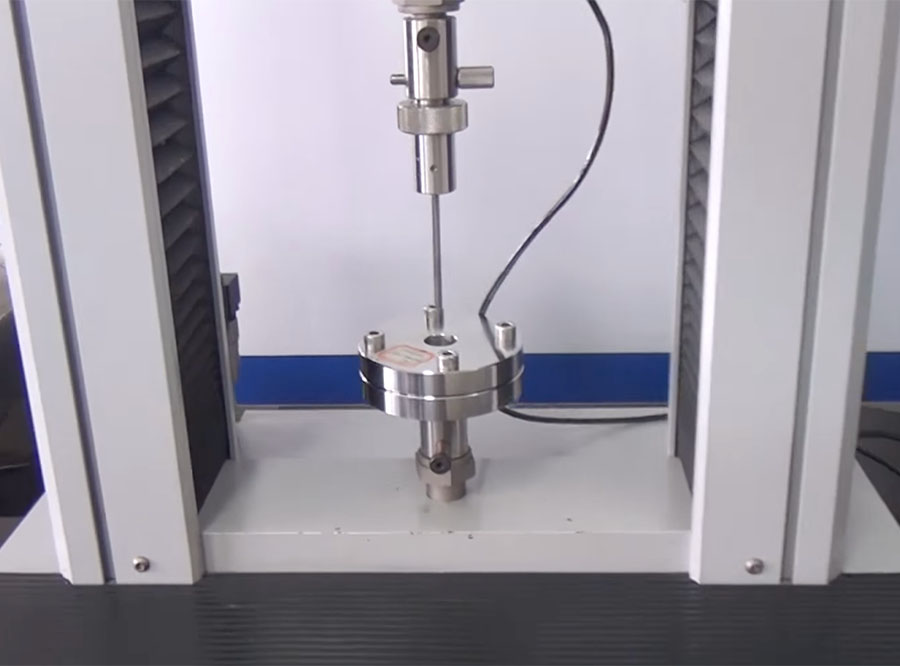
Puncture resistance testing helps ensure that gloves offer adequate protection against sharp hazards, reducing the risk of injuries such as puncture wounds and needle sticks. It is particularly important in industries such as healthcare, waste management, and recycling, where workers are exposed to sharp objects as part of their job duties.
Applications Across Industries
Cut resistant gloves find applications across a myriad of industries where workers encounter sharp objects and machinery. From manufacturing and construction to automotive and metalworking, these gloves are indispensable for safeguarding hands against potential injuries.
Professionals in the food processing, glass manufacturing, recycling, and healthcare sectors rely on cut resistant gloves to mitigate risks and uphold safety standards in their respective fields.
In conclusion, the selection and utilisation of cut resistant gloves are critical components of workplace safety strategies.
By understanding the intricacies of safety specifications, materials, testing procedures, and applicable industries, employers can make informed decisions to protect their workforce from potential injuries. Investing in high-quality cut resistant gloves not only fosters a safer work environment but also underscores the organisation's commitment to prioritising employee well-being.
Remember, proactive measures today can prevent accidents and injuries tomorrow.
- How Long Does PPE Last? (Probably Not As Long As You Think) - 12th March 2025
- BSIF Issues Urgent Warning: 90% of PPE from Non-Registered Providers Fails Safety Tests (2025) - 10th February 2025
- Understanding UK Safety Standards for Respiratory Protection - 14th October 2024